Achieve Uniform Coating Results with Slit Nozzle Solution
Author: Tan Yi Farn, Last update on May 26, 2025, Prepared by the NSW Automation Marketing Team
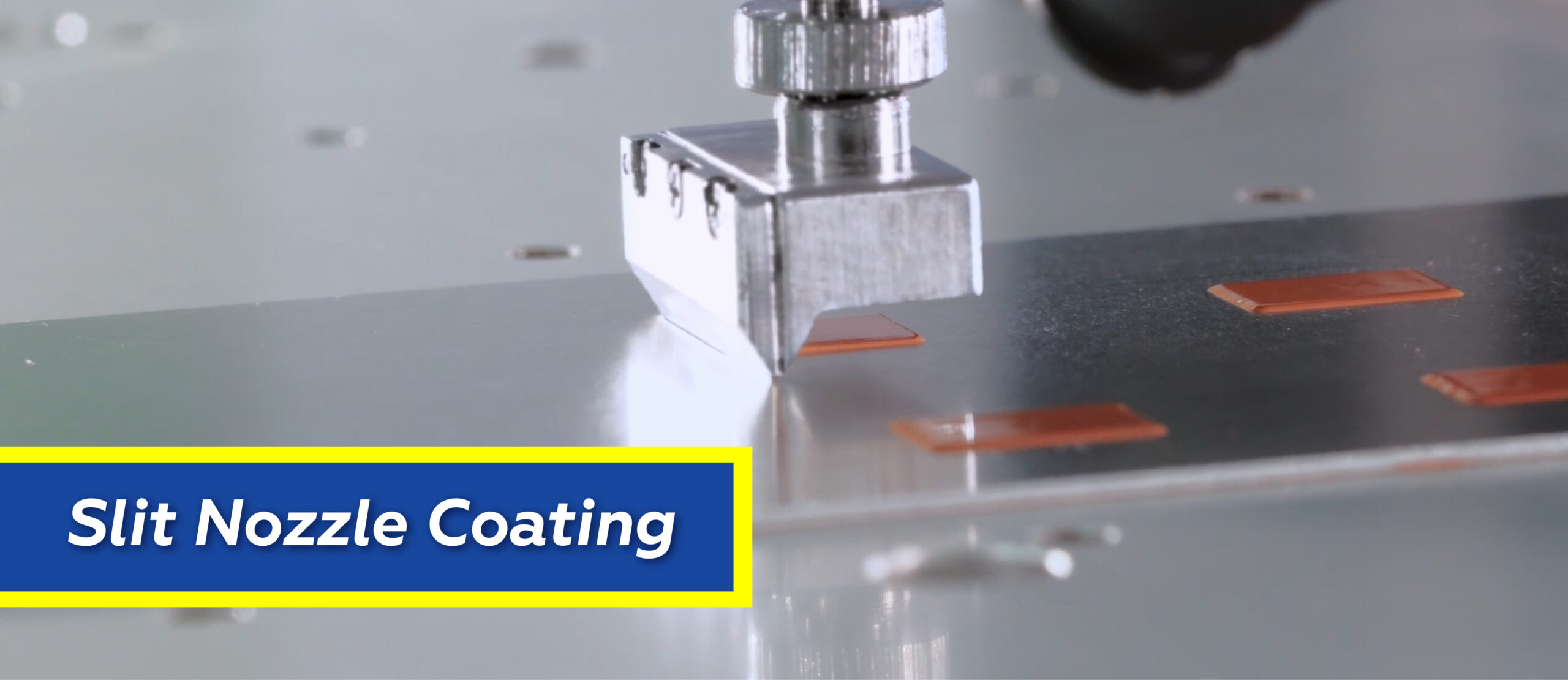
What is Slit Nozzle Coating?
Slit nozzle coating is an advanced technique widely used in electronics, display manufacturing, and high-precision coating applications. The slit-shaped nozzle distributes materials as a continuous sheet, ensuring uniform and precise coverage across the application surface.
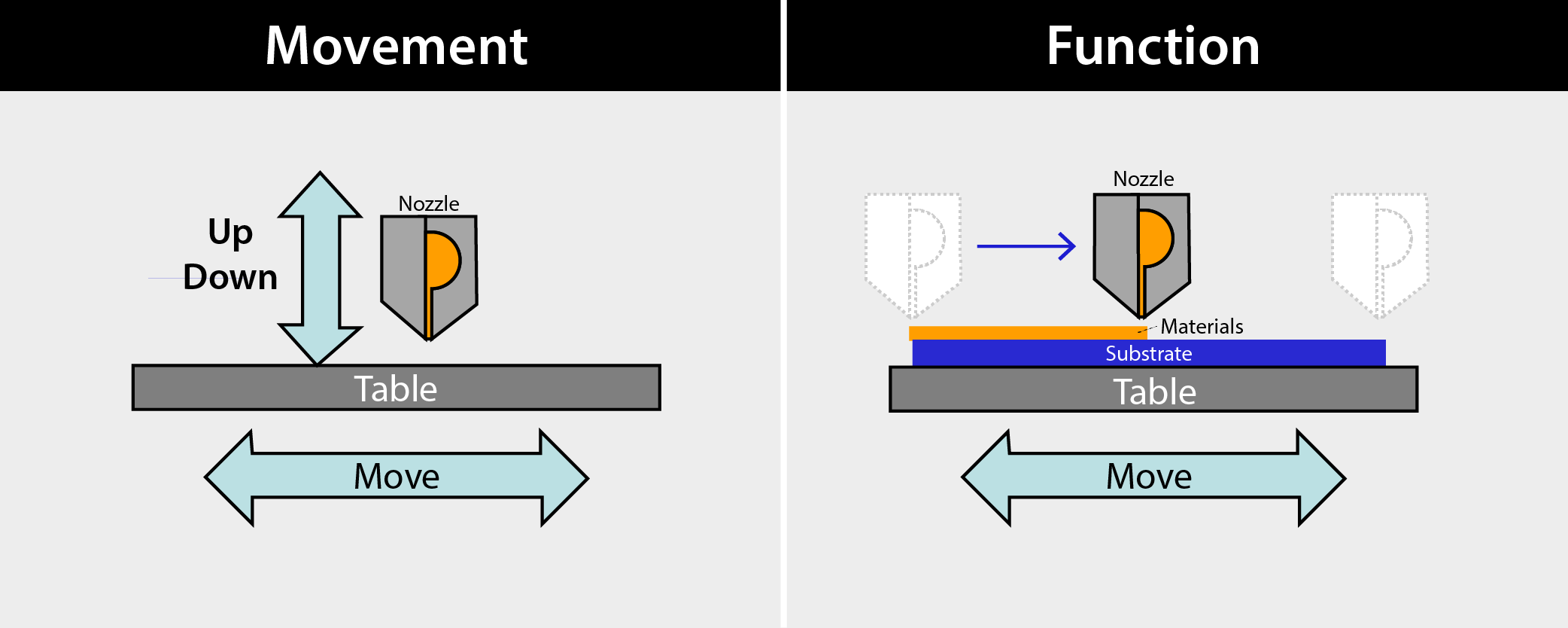
In slit nozzle coating, the nozzle moves up and down to control the coating thickness. While the table moves horizontally to spread the material evenly across the surface. This coordinated movement ensures a smooth, uniform layer, making it ideal for precise applications in electronics and display manufacturing.
Applicable in Industries
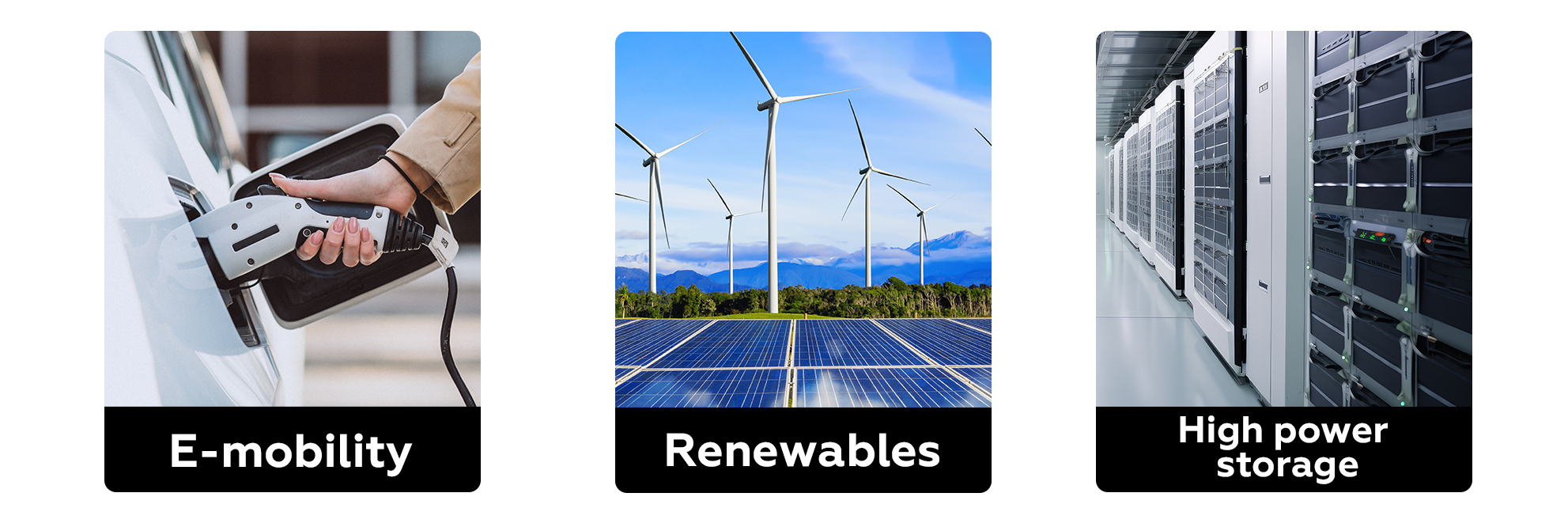
Hands-On Demonstration
In our demonstration, we used copper sintering paste with the slit nozzle coating method to highlight its effectiveness. This technique showcases the superior precision and efficiency of dispensing materials in a controlled manner.
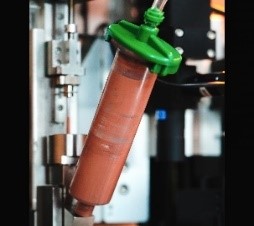
Copper Sinteering Paste
The Usage of Sinter
Material properties of sintered silver (Ag) or copper (Cu) offer significant benefits over traditional solder for certain applications. Sintered materials provide enhanced electrical conductivity, improved thermal performance, and a robust bond, making them ideal for demanding environments in the electronics industry.
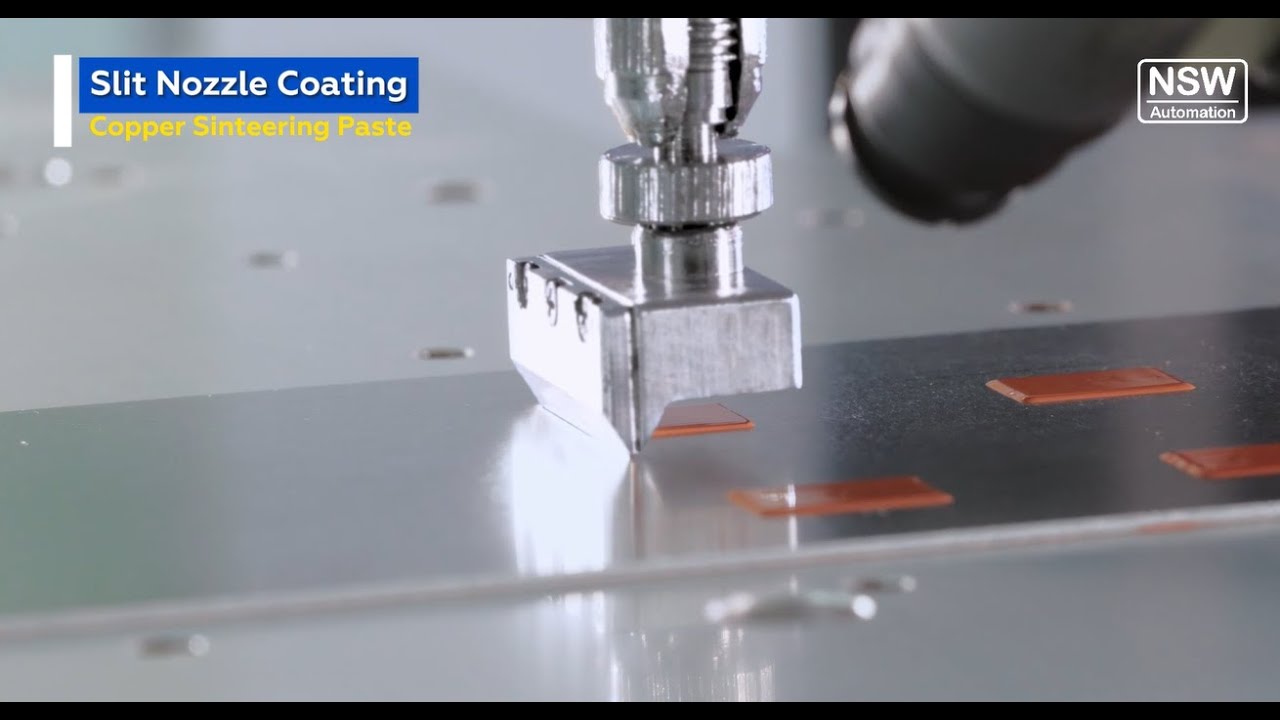
Sintering Process Copper Paste Slit Nozzle
Observations and Results
Our demonstration highlighted several key benefits of the slit nozzle coating method:
- High Precision
Achieves a coating thickness range of 100 μm to 1 mm, ensuring consistent and reliable application to meet diverse industry requirements. - Material Efficiency
Controlled flow significantly reduces waste and optimizes the use of coating materials. - Scalability
Effective on both large and small substrates, offering versatility for a wide range of applications. - High Throughput
Designed for mass production, ensuring continuous operation and efficiency.
Key Elements to Success
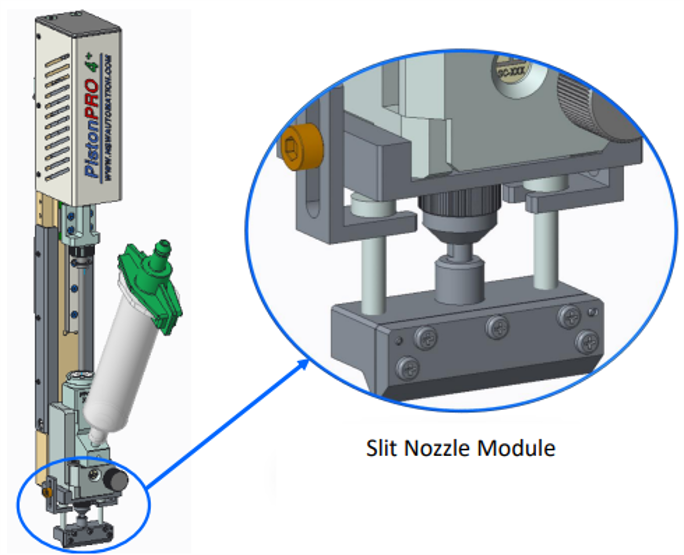
1. Slit Nozzle
This narrow, elongated orifice ensures precise and consistent flow of the coating material for uniform distribution and minimal defects, with shim plate variance available in 5 mm, 10 mm, 20 mm, and 40 mm configurations to suit different application requirements.
2. Gap Control Mechanism
The dispensing handler helped to control a fixed distance between the nozzle and the substrate, ensuring precise coating thickness and enhancing overall process accuracy, with a dispense gap configurable between 80 μm and 100 μm for precise application control.
3. Pump/ Reservoir
This component supplies the coating fluid to the nozzle at a regulated pressure, crucial for maintaining a stable flow rate and preventing disruption. Options include a volumetric pump or an auger pump, allowing for tailored solutions based on specific application needs.
• Volumetric control
• Positive displacement (linear actuator motor)
• Medium to High viscosity
• Process parameter control
• Back suck available
• Auger Screw Pump
• Large volume
• High viscosity
• Back suck available
Elevate Your Manufacturing with Slit Nozzle Solution
Achieve precise coatings, reduce waste, and optimize efficiency with our advanced technology.